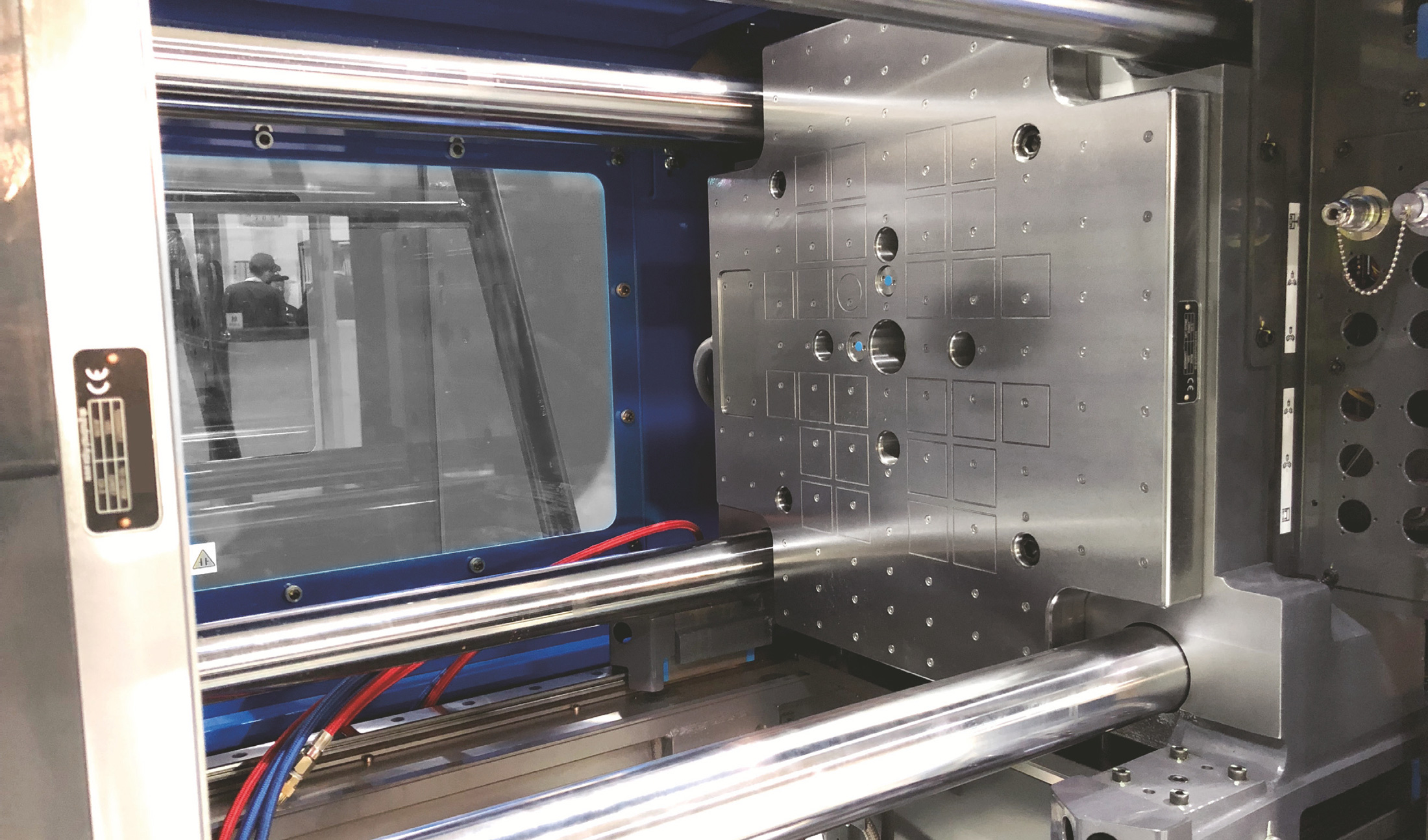
The Future Of
Quick Mold & Die Change
THE BEST SOLUTION FOR QUICK MOLD & DIE CHANGE
magbo is the product for quick mold change in injection mold presses, quick die change for stamping presses, and quick mold change for the die casting industry.
The electro-perm system does not use power once energized so a loss of power does not cause a loss of holding force. The technology, a safe and reliable magnetic circuit, is widely used on work holding, material handling, and mold / die clamping.
The advanced double magnet circuit is composed of square poles machined into a solid block of steel. Each pole generates a constant, uniform and predefined force regardless of who turns the system on. This force is proportional to the number of poles in contact with the die surface.
The magnets do not magnetize the entire mold / die, the magnetic flux penetrates the die only 20mm deep. The mold / die face and part cannot become magnetized, allowing for scrap removal, and proper die operation without interference. In a few seconds with the simple press of a button, it is possible to clamp or unclamp the mold / die in complete safety. Even during a power failure, the system remains operative, with constant clamping force.
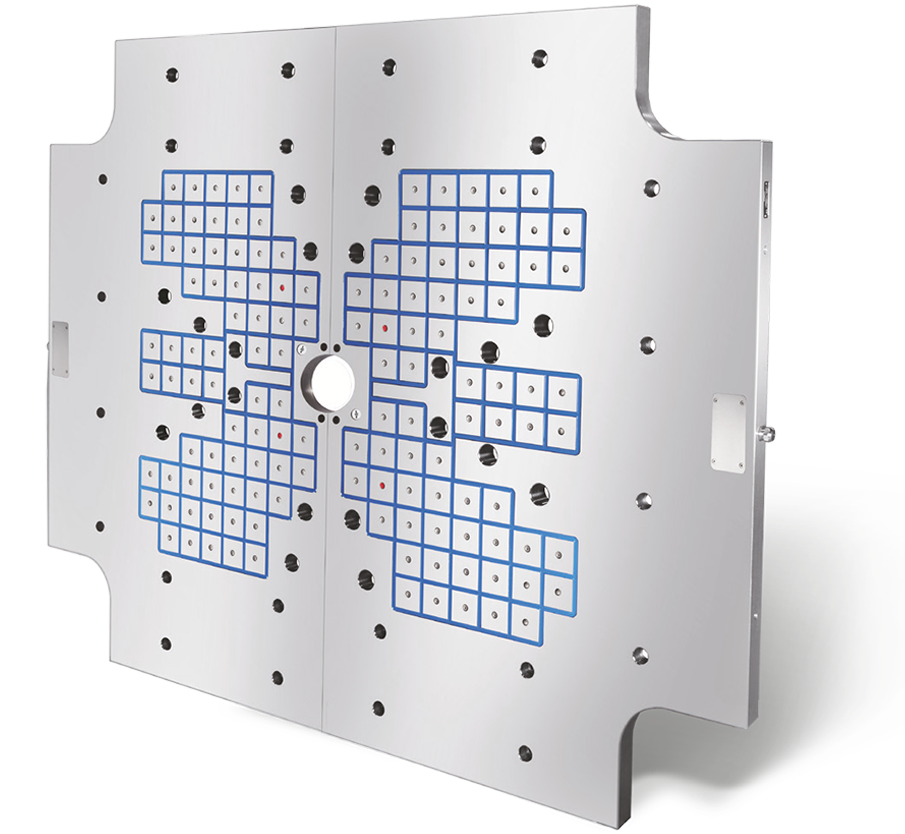
Soph offers the most comprehensive package of magnetic solutions for workholding, mold and die clamping and material handling. Starting the business in 1998, until now Soph owns the trademarks and business of BRISC, magbo and HELMHOLTZ which is for workholding, mold and die clamping and material handling respectively. Based in Hamburg Germany, after years of development, Soph now has branches in USA and China.
Our ability to provide immediate technical answers, immediate service, custom design, OEM specific products and product lines keeps us ahead of the curve.
With creative problem solving and application specific solutions, Soph is considered to be one of the finest sources for magnetic solutions available. We are dedicated to provide the best product with the best performance to match each application. By using customer input we are able to provide tailor made solutions using standardized products to create unmatched value in substantially shorter market cycles.
, THE BEST SOLUTION
Injection molding
MBP
Electro-Permanent Magnetic Quick Mold Change System
For Injection Molding Machine
magbo is currently the most comprehensive answer to the growing requirement of JIT (just in time), SMED (single minute die exchange) in all advanced manufacturing processes facing smaller batch runs and wider product ranges.
Metal Stamping
MBS
Electro-Permanent Magnetic Quick Die Change System For Stamping Presses
MBS is suitable for dies of any shape and size, with no modification.Die standardization is not necessary: savings in engineering time and overall cost.
Locating devices are easy to add, scrap holes can be used, bolster extensions can be added. Dies on parallels can be held with the special parallel pole design T-slots in the lower can be added to enable a wide variety of die lifter configurations.
One operator, with no tools, can operate all the Metal Stamping procedure easily and in total safety, outside the presss.
Rubber Molding
MBR
Electro-Permanent Magnetic Quick Mold Change System
For High Temperature Presses
The most effective and safe way to change die on high-temperature presses. Application for any size of die, no standardization of the mould back plates required. Possibility of integration of any type of heating system: rods, heating fluid, cables etc.
Can be applied in many industrial sectors such as:
– compression rubber
– aluminum – injection rubber
– composite
BLOW MOLDING
MBC
Electro-Permanent Magnetic Quick Mold Change System For Blow Molding Machine
Magnetic plate can be 30mm in thickness, maximize machine daylight saving.
Locating devices are easy to add. Compatible with multiple types of machines, including standard two platens machines, dual work-station and magnetic clamping for blow-pins. One controller can independently control up to 6 magnetic plates simultaneously, Efficiently reducing mold changeover time with streamlined simplicity and enhanced safety.
Increased PRODUCTIVITY with FASTER and SAFER mold & die challenge
Intrinsically Safe
An instantaneous electrical charge energizes the magnetic system. Once energized, the magnetic field will remain for an unlimited time.
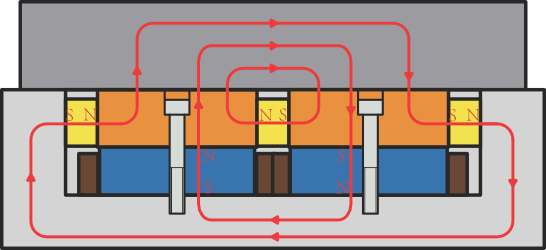
Magnetization
During the Mag phase, the magnetic flux is outside of the magnetic platen safely clamping the mold. The flux depth is limited to 1 inch so as not to affect any internal parts of the clamped mold.
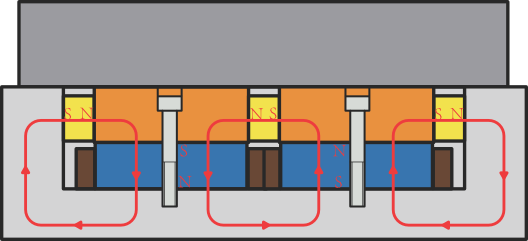
Demagnetization
During the DeMag phase, the magnetic flux is drawn back inside of the magnetic platen. This Demag Cycle leaves no residual magnetism in the mold allowing it to be removed easily from the machine for changeover.
Neutral Frame
The magbo® neutral frame magnetic system does not use the press as part of the magnetic loop under any circumstance.
This ensures the highest air gap / force performance and the easy installation and removal of the plates under any circumstance.
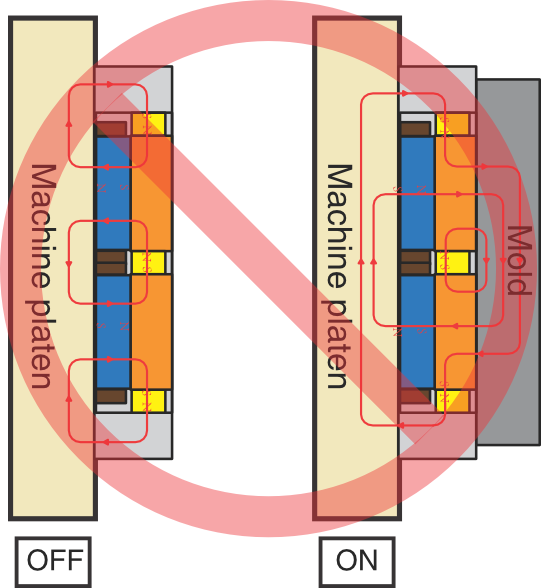
Better Air-gap Curve
Using an active north and south pole working together, magbo® generates more magnetic force over an air gap compared to our competitors.
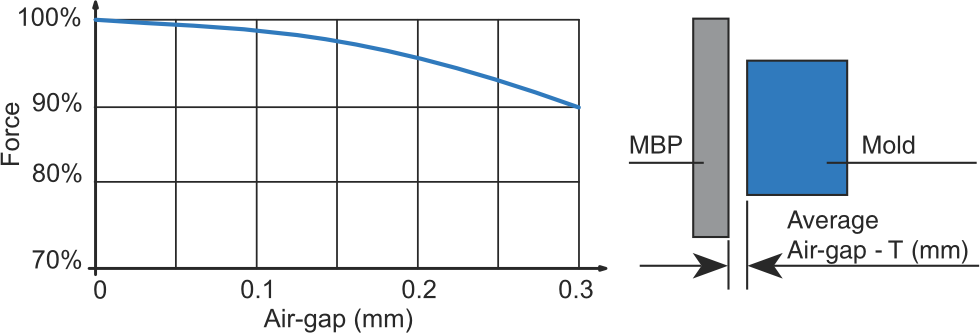