Applications
- Thermo set materials
- Rubber injection
- Composite compression
- Aluminium injection
- Rubber compression
- Magnetic platens can be ordered with T-slots to allow lifter installation
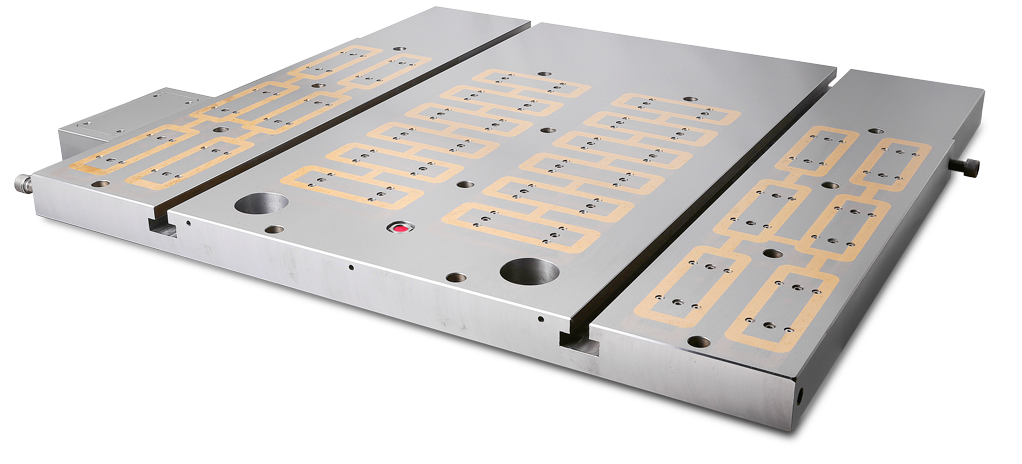
Less Mold / Die wear
Due to the clamping force being distributed over the entire surface of the mold it will be held flatter reducing wear on mating surfaces.
More productivity due to less downtime to the main mold.
Better heat transfer than perimeter clamping.
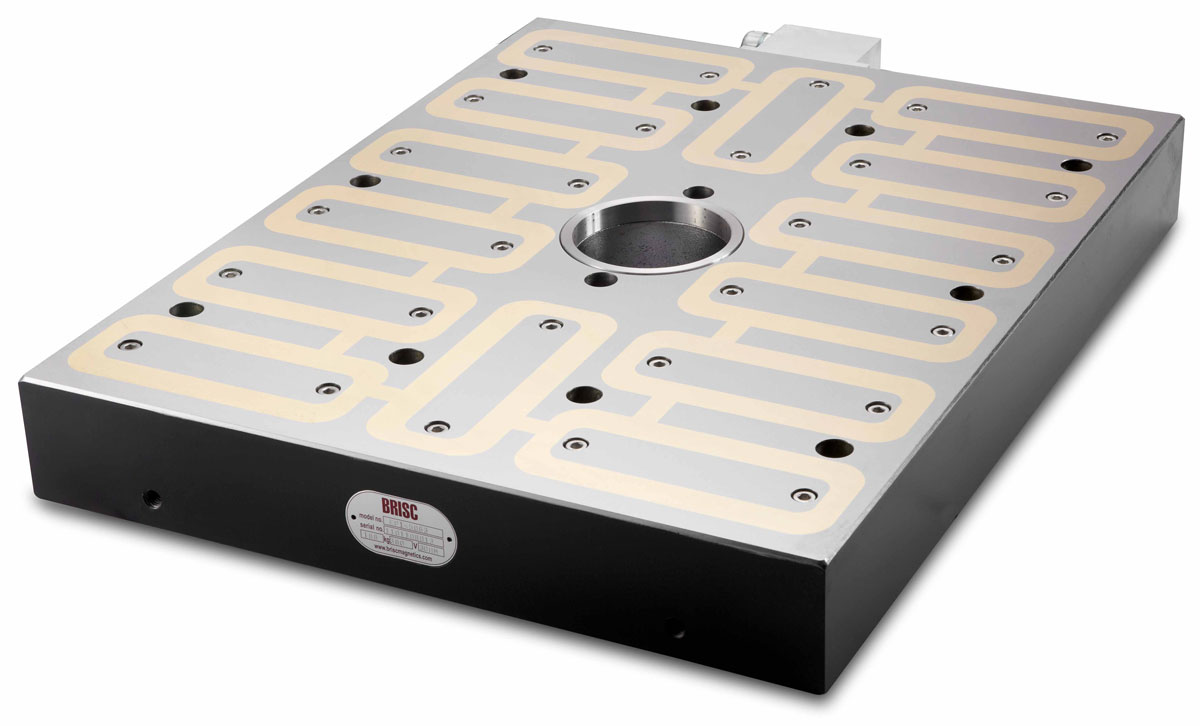
Powerful
The special magnetic circuit generates high power without leaving residual magnetism in the mold
Safe
The operator can clamp or unclamp the mold without ever touching it. Electro-perm technology requires no electrical energy during the operation of the machine. Loss of electrical power does not change magnetic holding force.
Labor saving
A single operator can clamp or unclamp a mold in seconds without ever touching the mold
Quick
Mold changes takes just a few minutes reducing down time to a minimum maximizing uptime
Main features
- Quick mold and die change
- Flexibility to accommodate any size or shape mold/die
- Universal machine interface
- Service temp to 250℃/482℉
- Optional built in heating
Flexible
Molds of any sizes and weights can be easily clamped to the machine platens in a few seconds without any modification.
Reliable
No moving parts, solid frame construction full metallic surface = a long maintence free life
Security measures
THERMAL SENSOR
Thermal sensor option can be integrated into e-stop
circuit.
KEY SWITCH
Key switch is in each remote control. Without key, system will not operate.
MSD SENSOR
Checks the magnetic quality of the mold
Checks the air gap which gives separate and redundant
safety when combined with a proximity sensor.
Double checks the current sensing system giving a
separate and redundant safety to the CSS system as well.
CSS SENSOR
CSS sensor checks the current passage from the main discharge cables to the magnetic platen.
PROXIMITY SENSOR
An inductive proximity sensor located in the “neutral” area detects the presence of the mold to enable the activation of the magnetization cycle. The 0,3 mm (0.012 in) threshold value prevents any “open field magnetization” to grant the operator safety and it immediately halts the machine functions in case of mold detachment. The full safety for the operator is also granted.
BDC SENSOR
Bottom dead center interlock prevents de-mag unless the press is closed.
MOLD CHANGE MODE
Only activated in Mold change mode/Die set mode
- One operator, with no tools, can operate all the die-clamping procedures easily and in total safety, outside the press.
Easy installation
Only a few bolts are needed to fix the magnets to the machine platens. The interface with the machine follows the international safety EUROMAP/SPI/JIS standards.
No die modifications
MBR can hold molds or dies of any size or shape.
MBR creates cost saving by reducing engineering time compares to other clamping methods.